Defect Tolerance Assessment (DTA) and Life Assessment of Turbine Rotor
Defect Tolerance Assessment (DTA)
I ( Ninh Nguyen) have had and two articles presented at the WTIA and IEAust conferences and published in the WTIA welding journals.
Fitness-for-service and defect tolerance assessment solutions for cracked components to remain in service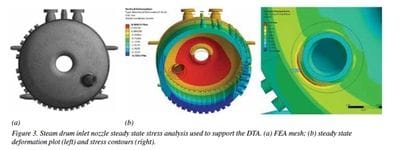
This paper describes the application of the FFS/DTA methodology to assist plant asset managers in dealing with cracks that
have been detected in in-service components, particularly those in the power, petrochemical, mining and transport industries.
Several state-of-the-art structural integrity assessment procedures such as AS/NZS 3788, BS7910, R5-R6 and API-579-1/
ASME FFS-1 are described and discussed; and their application to practical situations using the principles of FFS/DTA is illustrated
through a series of selected case studies. The usefulness, effectiveness and versatility of this fracture-mechanics based
methodology for examination of in-service cracked components is amply demonstrated.
Featured in the Australasian Welding Journal Welding Research Supplement
Remaining life assessment of a high pressure turbine rotor
This paper describes finite element and fracture mechanics based modelling work that provides a useful tool for evaluation of the remaining life of a high pressure (HP) steam turbine rotor that had experienced thermal fatigue cracking. An axis-symmetrical model of a HP rotor was constructed. Steam temperature, pressure and rotor speed data from startups and shut downs were used for the thermal and stress analysis. Operating history and inspection records were used to benchmark the damage experienced by the rotor.
Fracture mechanics crack growth analysis was carried out to evaluate the remaining life of the rotor under thermal cyclic loading conditions. The work confirmed that the fracture mechanics approach in conjunction with finite element modelling provides a useful tool for assessing the remaining life of high temperaturecomponents in power plants.
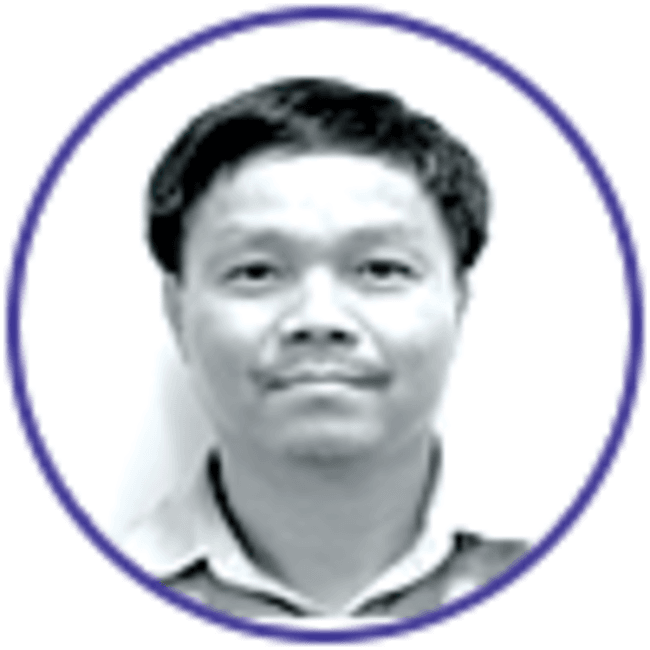)
Tags:Analytical ServicesEnvironmentRisk Based Assessments |