A major fire at a mine caused significant damage to various structural members of a dredger, however the severity of this damage was unknown. The client required a quick method to determine if the steel members had sustained critical or superficial damage.
CrackSizer Case Study
HRL saves major mine substantial material and labour costs using CrackSizer®
Challenge
Solution
HRL was engaged by the client and deployed CrackSizer®, its innovative electromagnetic inspection method, used primarily to detect and size surface breaking defects in power station components. In this case however, HRL leveraged this electromagnetic capability to function as a rapid hardness detection tool. Scans of the suspect members effectively identified where the real damage had occurred, versus superficial surface coating damage. Using a portable hardness tester, HRL then verified the drop in hardness, which corresponds to a loss of material strength.
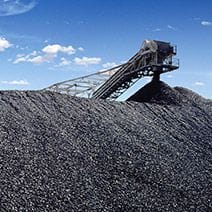
Results
Though the principal function of CrackSizer® is to identify and size crack defects, HRL was able to expand its capabilities by utilising its scanning signal to identify changes in the microstructure and material properties of metals. This inspection method reduced site preparation time and minimised access requirements, significantly reducing the outage time required. As a result of the comprehensive CrackSizer® testing done by HRL, the client only had to replace the critically-damaged members, saving them substantial material and labour costs.