High Energy Piping Refloat Case Study
HRL engineers tailored a solution for the client which substantially increased the future safe operation of their piping system
Challenge
Solution
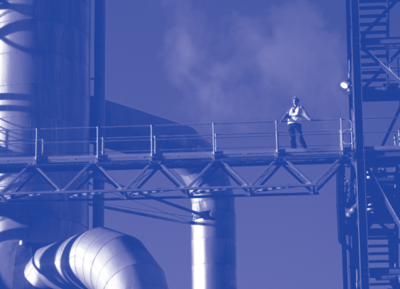
expertise in action
Contact our technical consultants
Call us
or
Email us to get started today.
NATA accredited AtS/NZS ISO 17025, AS/NZS ISO 17020NATA Accredited Laboratories number 561
ISO 9001 Quality Management certified by BSI under certificate number FS605116.